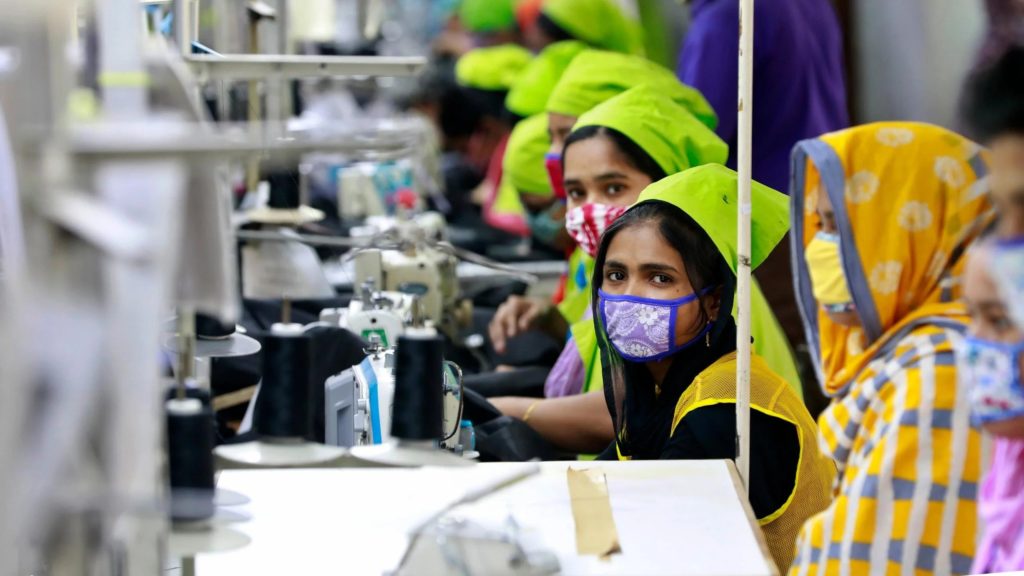
Enhancing the Lives of Workers in the Bangladesh RMG Sector: A Path to Progress
Originally published on the LightCastle Partners website.
The RMG Sector Navigating Global Challenges
The Bangladesh RMG industry, a leading global apparel sourcing hub, employs more than 4 million workers and contributes 10.35% to the GDP, with a 7% annual growth. Despite being the second-largest garment exporter globally, the industry faced a significant setback during the COVID-19 pandemic, experiencing a USD 3.16 billion loss in orders and supply chain disruptions due to reliance on China for 67% of raw materials (RMG Bangladesh, 2023).
While recovering from the pandemic’s impact, the industry now grapples with challenges stemming from global inflation linked to the Russia-Ukraine conflict, affecting key export markets like the USA, UK, and EU. On a positive note, the sector has seen a promising 32.19% growth in exports to non-traditional markets, including Japan, South Korea, and India, offering a glimmer of hope for recovery. (Mirdha, 2023)
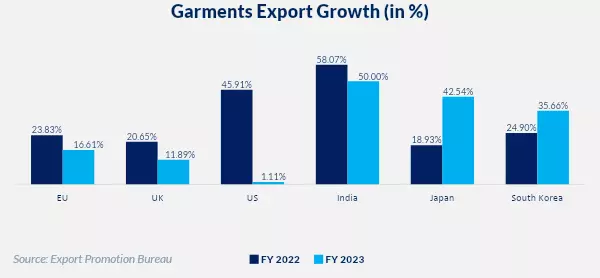
However, the Bangladeshi RMG industry thrives on its competitive edge rooted in low labor costs, a key factor enabling it to stay globally competitive. In the face of relentless efforts to minimize labor costs amidst the growing challenge of inflation, one must wonder: does the current minimum wage for RMG workers adequately sustain their well-being and livelihoods in this competitive industry landscape?
RMG Workers’ Struggle Amidst Inflation
In the backdrop of workers grappling with a static BDT 8,000 minimum wage established in 2018, a recent development by the government’s wage board turned the workers’ anticipation into discontent. As of November 7, 2023, the minimum wage for RMG workers was increased to BDT 12,500. While this adjustment represents a notable improvement, it remains shy of the workers’ ambitious call for BDT 23,000. This development led to further protests by RMG workers as they had higher hopes from the government. (Khatun, 2023)
Adding to their plight, a recent 51% hike in fuel oil prices caused commodity prices to skyrocket, making essentials unaffordable for RMG workers. As per Ms. Kalpona Akter, Executive Director at Bangladesh Centre for Workers Solidarity, the salary of garment workers increases by 5% annually, while commodity prices are increasing at a much higher rate.
Sharif, a worker from SF Washing Ltd at Kanchpur, shared his struggle, revealing that rising prices forced him to abandon chicken purchases for the last three to four months, opting for low-quality fish options like Tilapia and Pangash. (Hossain, 2022)
While workers like Mr. Sharif, advocate for wage increases to cope with the soaring cost of living, RMG owners, despite acknowledging the pressure on workers, cite increased expenses, including fuel, electricity, and prices and 5% annual salary increments, as barriers to wage hikes. (Hossain, 2022)
A Holistic Look at the Wellbeing of RMG Workers
Although BDT 12,500 falls short of supporting the overall well-being of workers, it is to be noted that this applies primarily to newcomers without experience. With training and experience, as these workers move up the grades, they see increases in their wages, which, when coupled with overtime payment, well exceed the minimum wage, providing a more substantial income.
Furthermore, RMG workers’ welfare extends far beyond their paychecks. With nearly half their day spent at work, the workplace must provide facilities that enhance overall well-being. Some of the most prevalent facilities, across the industry, have been highlighted below:
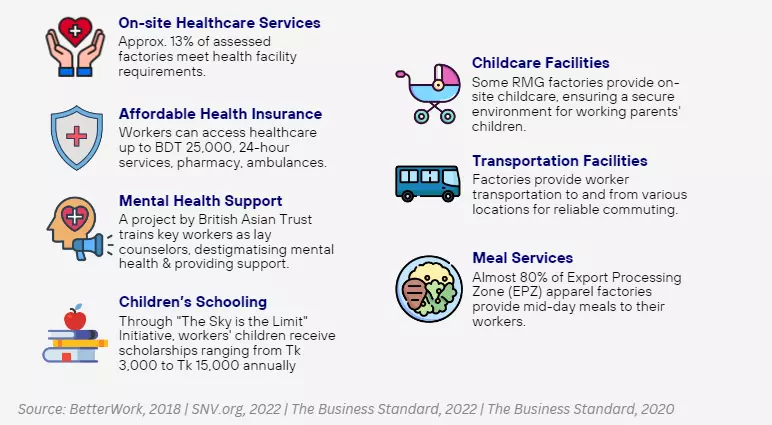
Impediments to Workers’ Welfare
Despite some positive initiatives aimed at improving the welfare of RMG workers in Bangladesh, various challenges continue to impede the well-being and progress of this critical workforce. The challenges faced by RMG (Ready-Made Garments) workers in Bangladesh span across various dimensions, significantly impacting their overall well-being. In terms of Health and Nutrition, these workers grapple with adverse conditions such as prolonged working hours, inadequate lighting, poor ventilation, and overcrowded toilet facilities, all of which contribute to detrimental effects on their physical and mental health.
Moreover, a Safe and Healthy Environment is compromised as workplace harassment, particularly from supervisors, affects a substantial percentage of RMG workers. (Md. Nazim Uddin Bhuiyan FCMA, 2019)
Additionally, concerns about fire accidents are prevalent due to insufficient safety precautions. Economic Empowerment remains a critical issue, with high turnover rates, unclear overtime pay, and widespread dissatisfaction with low wages hindering the workers’ financial stability and growth.
In the realm of Equality, Acceptance, and Social Rights, discrimination, and harassment, often perpetuated by supervisors, impact the social rights of these workers, exacerbated by a lack of awareness about labor laws. Lastly, in terms of Education and Professional Development, high turnover rates and limited awareness of labor laws impede skill development among RMG workers, necessitating external support for essential needs like healthcare and education. (Md. Nazim Uddin Bhuiyan FCMA, 2019)
As Bangladesh grapples with challenges in its garment industry, it’s enlightening to examine the improving conditions in neighboring countries. In Vietnam and China, strides in worker well-being, safety initiatives, and economic empowerment underscore the potential for positive transformation in the region.
For instance, In Vietnam, the garment industry emphasizes worker well-being through initiatives like the Better Work Vietnam program, jointly led by the International Labour Organization (ILO) and the International Finance Corporation (IFC). This program focuses on creating safe and healthy working conditions, promoting economic empowerment through skill development, and ensuring gender equality in the workplace (Better Work Vietnam, 2022; ILO, 2023). (BetterWork Vietnam, 2023)
Similarly, In China, the government focuses on workplace safety regulations, economic empowerment through skill training, and initiatives promoting gender equality and social rights in the garment industry (The Lancet, 2019)
As the RMG industry in Bangladesh confronts obstacles spanning health, safety, and economic stability, comparing these challenges with the progress in neighboring countries like Vietnam and China sheds light on potential improvement avenues. Despite ongoing efforts to enhance worker wellbeing, the stark reality persists: RMG workers in Bangladesh grapple with making ends meet due to lower wages.
Factors Deterring Adequate Wage Increase
Despite the establishment of a wage board in April 2023, the recent development was rather slow to come. This delay has been attributed to global economic liquidity issues. (The Business Standard, 2023)
Besides, concerns about the impact on cost competitiveness persist, especially as Bangladesh approaches LDC graduation in November 2026, risking the loss of preferential trade benefits. (Khan, 2023) With 85% of exports coming from the RMG sector, maintaining competitiveness is crucial to avoid significant economic impact.
This begs the question: Is there a viable path for the Bangladesh RMG industry to harmonize worker well-being through fair wages while preserving its global competitive edge?
Striking a Balance: Wellbeing and Competitiveness in RMG
Bangladesh’s RMG sector, claiming the spot as the second-largest apparel exporter, relies on the advantage of the lowest minimum wages in the apparel sector (The Business Standard, 2023). However, the sustainability of this strategy is in question, as the pursuit of low costs, primarily through minimal wages, poses a significant threat to the well-being of the workers driving this economic engine. As the country navigates global competition, the ethical considerations of its wage policies warrant a closer look.
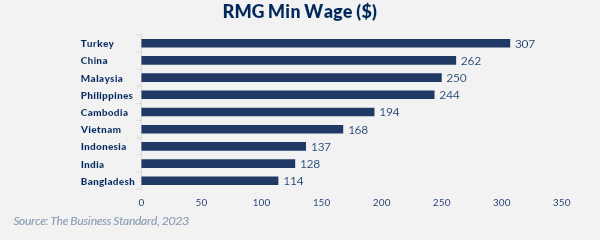
Besides, although Bangladesh has been at the forefront in terms of labour costs, it has been lagging behind in terms of productivity compared to the competing countries. As per Asian Productivity Organization, Bangladeshi RMG workers had the lowest per hour labour productivity in 2019.
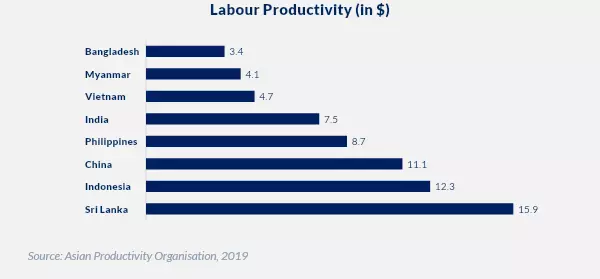
Insufficient training, low wages, poor nutrition access, subpar living conditions, and inadequate work environments are linked to low worker productivity. Professor Mustafizur Rahman at CPD warns that labor and capital productivity improvements are vital as Bangladesh progresses and enters the Fourth Industrial Revolution (Hossain, 2021)
As per the Bangladesh Institute of Development Studies (BIDS), a skill gap of over 60% exists in the RMG sector, ranking second highest among all industries (The Business Post, 2023).
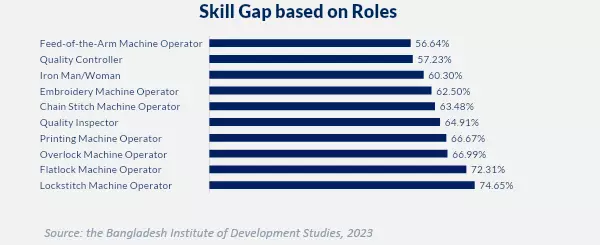
Keeping this in mind, to ensure the sector’s sustainable growth, the study proposes the implementation of job-specific training programs in partnership with organizations like the Skills for Employment Investment Program (SEIP), professional bodies, and employers.
Notably, the study identifies machine operators as having the most pronounced skill gap, underscoring the importance of targeted training initiatives in this area to boost overall industry productivity and competitiveness. (The Business Post, 2023)
This study emphasizes the importance of not only providing training to employees but also ensuring the provision of suitable facilities such as improved working conditions, safety measures, and access to nutritious food. These factors are crucial for enhancing the overall well-being, and subsequently, the productivity of workers, which, in turn, will help the Bangladeshi RMG industry to remain globally competitive without putting pressure on labour costs.
The Way Forward for the RMG Sector
As the Bangladesh government charts the path forward for the RMG sector, several strategic initiatives have been devised to bring about transformative changes. These initiatives include (Bangladesh National Productivity Master Plan FY2021-FY2030, 2019):
- Transformation of Large RMG Enterprises:
The government plans to transform large RMG enterprises into high-value, capital-intensive operations, ensuring stable employment and improved working conditions with safety enhancements.
- Enhancement of the Entire Value Chain:
The government plans to enhance the RMG value chain, offering workers professional development opportunities and skills advancement. A focus on technology adoption and R&D is likely to improve working conditions and foster skill development.
- Progression from Low-Value to High-Value Production:
The government is actively promoting the shift from the traditional “cut-make-trim” production model to high-value garments, responding to industry demands. To address the threat of potential job displacement, upskilling, and reskilling of RMG workers are required. This not only enhances their professional development but also ensures their relevance in the evolving industry while improving product quality and working conditions for a more sustainable RMG sector.
- Investment in R&D and Skill Development:
RMG manufacturers are encouraged to invest in research and development and develop local design and pattern-making capabilities. Increased investment in R&D fosters innovation and improved product quality, providing RMG workers with opportunities for skill development and higher-quality output.
- Strengthening Backward and Forward Linkages:
The government strives to reinforce both backward and forward linkages in the RMG sector, improving value chain efficiency. This results in reduced downtimes, enhanced productivity, and a more stable work environment with potential wage improvements for RMG workers.
Policy Recommendations to Improve Working Conditions
A number of policy recommendations have been proposed, with an aim to enhance the well-being of RMG workers in Bangladesh by addressing wage, safety, and service access concerns. The goal is to improve working conditions for these dedicated industry contributors. (Bangladesh Institute of Labour Studies, 2023)
- Minimum Wage Standards: Establish and regularly review minimum wage standards for RMG employees to combat income inadequacy. Implement a framework for periodic wage assessments and adjustments, ensuring fair compensation for their labor.
- Training and Skill Development: Provide comprehensive training and education programs for RMG workers. These programs should focus on skill enhancement, improved productivity, and adaptation to modern technologies. Include essential life skills, such as financial literacy and negotiation skills, to empower workers and broaden their career prospects.
- Safe and Healthy Working Conditions: Enforce and uphold policies that guarantee safe and healthy working environments. These policies should encompass proper sanitation facilities, adequate rest breaks, and suitable living accommodations. Employers must be mandated to provide the necessary supplies and equipment to enhance task performance and overall well-being.
Given the significant impact of the European Union (EU) on Bangladesh’s RMG industry (comprising 44.6% of total exports in FY 2022), it is crucial for Bangladesh to prioritize and implement these recommendations. The EU has stringent regulations that prioritize safeguarding worker rights, making it essential for Bangladesh to not only secure EU contracts but also to improve working conditions comprehensively. (LightCastle Analytics Wing, 2023)
In conclusion, RMG workers in Bangladesh face challenges like low wages and safety concerns, but efforts to improve their well-being are growing. Government strategies, including skill enhancement and product diversification, offer a promising path to a more sustainable future. Continued investment in training, better conditions, and innovation is vital for the long-term prosperity of these key contributors to Bangladesh’s economy. Furthermore, efforts should be put in to fill the gaps in other industries as well, where the standards can be even further behind the RMG industry, due to a lack of scrutiny. The current standards of the RMG factories can contribute a lot to all other industries to level up.
Author:
This article was authored by Raisa Mahjabin, a Content Writer at LightCastle Partners. Advisory and editorial support was provided by Samiha Anwar, Business Consultant at LightCastle Partners. For further clarifications, contact here: [email protected]
References:
- Asian Productivity Organization. (2019). Bangladesh National Productivity Master Plan FY2021-FY2030. ASIAN PRODUCTIVITY ORGANIZATION.
- Bangladesh Bank. (2023). Quarterly Review on Readymade Garments (RMG): April-June of FY23 . Bangladesh Bank.
- Bangladesh Institute of Labour Studies. (2023). Policy Brief on: Protecting the Rights of Domestic Workers in Bangladesh. Bangladesh Institute of Labour Studies.
- BetterWork Vietnam. (2023). Better Work Viet Nam Annual Report 2023: An Industry and Compliance Review. International Labour Organisation.
- Hossain, R. (2021, October 22). RMG’s low labour productivity a major post-LDC challenge. Retrieved from The Business Standard
- Hossain, R. (2022, August 20). RMG workers struggle to survive rising commodity prices, owners say they are in hard times too. Retrieved from The Business Standard
- International Labour Organisation. (2022). Employment, wages and productivity trends in the Asian garment sector. International Labour Organisation.
- Khan, M. S. (2023, May 30). The low-wage specialisation niche in Bangladesh is not a long-term solution: UN Special Rapporteur. Retrieved from The Business Standard
- Khatun, F. (2023, November 20). What’s stopping RMG workers from getting higher wages? – Fahmida Khatun from the Centre for Policy Dialogue
- LightCastle Analytics Wing. (2023). The EU’s Due Diligence Act: Way Forwards for Bangladesh’s Apparel Industry. Retrieved from LightCastle Partners
- Md. Nazim Uddin Bhuiyan FCMA, A. D. (2019). The Problems of Garments’ Workers in Bangladesh: A Survey from the Institute of Cost and Management Accountants of Bangladesh.
- Mirdha, R. U. (2023). Economy. Retrieved from The Daily
- RMG Bangladesh. (2023). RMG turns to India from China to get cheaper man-made yarn. Retrieved from RMG Bangladesh
- The Business Post. (2023). RMG sector has over 60% skills gap: Study. Retrieved from The Business Post
- The Business Standard. (2023, September 30). Six months on, still no progress in setting new wages for RMG workers. Retrieved from The Business Standard
- The Lancet. (2019). Improving occupational health in China. The Lancet.